
Pictured: A live, automated orbital welding process. The welding power supply provides electrical alternating or direct current (AC or DC) between the base metal and the welding electrode. An electric arc is formed where metal is melted and manipulated.
Since there are several diverse metals and fabrication applications, there are different arc welding processes, each with specific configurations, components, behaviors, and specialties.
The most common arc welding processes include:
- Gas Metal Arc Welding (GMAW) or Metal Inert Gas (MIG) Welding
- Gas Tungsten Arc Welding (GTAW) or Tungsten Inert Gas (TIG) Welding
- Shielded Metal Arc Welding (SMAW) or Stick Welding
- Flux Core Arc Welding (FCAW)
Gas Metal Arc Welding (GMAW) or Metal Inert Gas (MIG) Welding
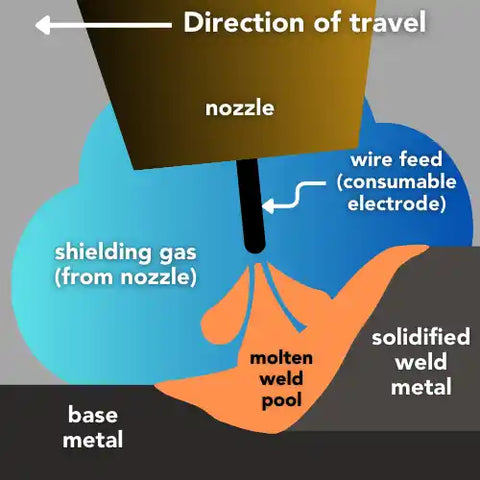
GMAW or MIG Weld process illustration.
The GMAW or MIG welding process uses a continuous wire feed as a consumable electrode, simultaneously acting as both the electrode and the filler metal. The arc melts both base metal and the wire feed in the presence of an inert shielding gas provided by the nozzle. Shielding gas protects the arc and molten weld pool from atmospheric contamination: other gases, such as nitrogen, CO2, and H20 vapor, can detract from arc stability, proper weld penetration, and sound mechanical properties upon weld completion.
GMAW is an efficient and versatile process. It can weld steel, stainless steel, copper, aluminum, and other metals in automated and manual welding processes. GMAW is commonly used in the automotive, manufacturing, ship/rail, and other high-production industries. With long production runs, finding oil and grease on base metals in these environments is expected. Fast deposition rates and environmental factors cause GMAW to produce smoke and spatter.
Gas Tungsten Arc Welding (GTAW) or Tungsten Inert Gas (TIG) Welding
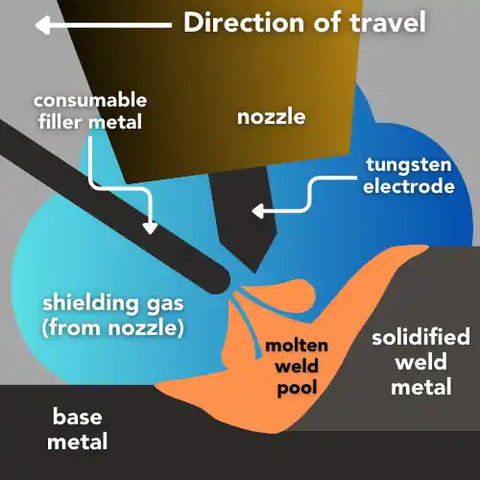
GTAW or TIG weld process illustration.
Unlike GMAW, the GTAW or TIG welding process uses a non-consumable tungsten electrode to create the arc between the base metal and the welding torch. Additionally, GTAW uses a separate consumable filler metal fed into the molten weld pool to build up the weld joint. Like GMAW, GTAW also feeds an inert shielding gas through the torch nozzle to help protect the arc and molten weld pool from atmospheric contamination.
GTAW is a high-quality and precise process. Slower deposition rates from lower torch travel speeds and less filler metal consumption tend to produce less spatter and high-quality welds. This allows for more precise torch control to weld small and intricate materials commonly found in the aerospace and tube manufacturing industries. Also, changeable electrode sizes and shapes allow both automated and manual GTAW processes to be highly versatile.
Shielded Metal Arc Welding (SMAW) or Stick Welding
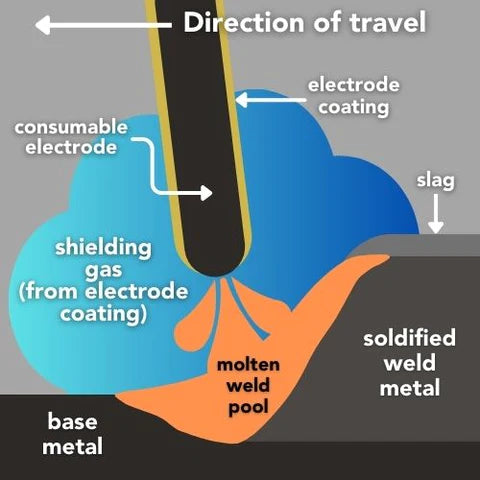
SMAW or stick weld process illustration.
SMAW, or stick welding, is a manual process where a consumable electrode stick acts as the filler metal and the origin of shielding gas. As the arc melts the base metal and stick electrode, it releases shielding gas and flux, protecting the live weld from contamination. The flux that rises and hardens on the weld surface is called slag.
SMAW is a simple, manual process. A welder can quickly set up and weld ferrous metals with a power supply, stick electrodes, and ground/electrode cables. This simplicity makes SMAW one of the world’s most popular manual welding processes. Like GMAW, stick welding produces smoke and spatter, but its simplicity makes it popular in many small manufacturing businesses, welding shops, and some outdoor applications.
Flux Core Arc Welding (FCAW)
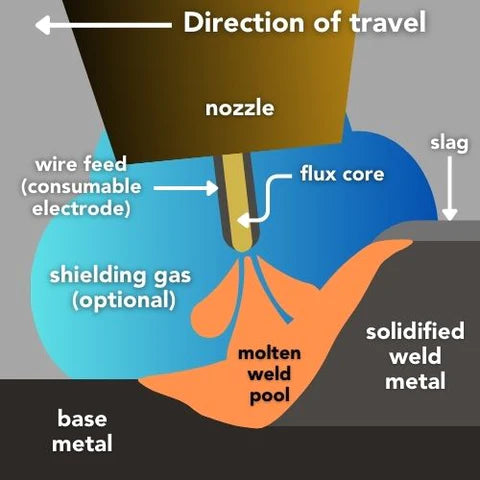
FCAW process illustration.
The FCAW process is similar to GMAW: both use a continuous wire feed that is a consumable electrode and filler metal. FCAW may or may not use shielding gas from the nozzle, but the main difference is the consumable wire feed contains a flux core that is the primary anti-contaminant agent. Like SMAW, the FCAW produces slag on the weld surface after cooling.
FCAW is a robust process. The automatic wire feed, flux, and optional shielding gas combination enable FCAW to endure harsh welding conditions as found outdoors or underwater. High deposition rates and penetration also make this process ideal for welding thick base metals in pipelines and ship hulls.
Arc Weld Viewing: The Cavitar Welding Camera
Regardless of the process, a live weld arc is inherently challenging to view, let alone record on video. All welding arcs produce enough intense visible light, UV, and infrared radiation to damage human eye and skin tissue. This same energy will render most cameras useless in viewing and recording video and images of GMAW, GTAW, SMAW, or FCAW.
Finding a high-quality, versatile weld camera is challenging as well. The different inherent arc welding properties - GTAW’s small arc size, GMAW’s smoke and spatter production, or SMAW’s numerous angles - leave most cameras limited to only working well with a single welding process.
The Cavitar C400-H Welding Camera proves highly versatile for capturing live arc welding, no matter which process.
- Full-HD resolution of 1440 x 1080 pixels up to 70 fps - captures the GTAW micro welds with clarity and ease.
- Replaceable spatter shields and cooling options - position close to GMAW or FCAW processes and see through the smoke and spatter
- Mounting and positioning options - Position the camera for enhanced educational value or social media content creation.