Behind every commercial airline flight lies a complex network of maintenance, repair, and overhaul (MRO) operations that ensure the aircraft remains airworthy. MRO may not always be the center of attention in aviation news, but it plays a crucial role in the aviation and aerospace industry by enhancing aircraft longevity, operational efficiency, and ultimately pilot and passenger safety. The following examines different types of MRO and the technology involved to ensure safe flights.
What is MRO?
MRO refers to the maintenance, repair, and overhaul processes necessary to keep aircraft in optimal operating condition. It encompasses a wide range of operations, from routine inspections and minor repairs to major overhauls and component replacements. MRO professionals conduct these tasks regularly to comply with stringent Federal Aviation Administration (FAA) safety regulations and guarantee the aircraft's reliability.
Maintenance
Aircraft maintenance checks are mandatory periodic assessments required for all civilian and commercial aircraft following specific time intervals or usage. The principal aim of these routine checks is to maintain the aircraft's safety and airworthiness.
In the United States, the FAA sets stringent safety and maintenance criteria for commercial airline companies. These regulations guarantee that all aircraft fulfill elevated safety requirements before they take flight. As a part of the FAA's regulations, commercial airline companies must establish and maintain a Continuous Airworthiness Maintenance Program (CAMP).
There are multiple types of maintenance checks occurring both on the ground and in the air; however, aircraft maintenance checks fall into four sub-levels of maintenance: A, B, C, and D checks.
A Check
An “A” check is performed within an aircraft hangar and is typically performed every 400–600 flight hours or 200–300 flight cycles, depending on the aircraft type. These checks include carefully examining the aircraft's body to ensure no damage, deformation, corrosion, or missing parts. Some other tasks technicians conduct involves changing filters, checking the pressure in tires and hydraulic lines and inspecting all emergency equipment. These checks take a minimum of 10 hours and are crucial for preventative aircraft maintenance and ensuring safe aircraft operation.
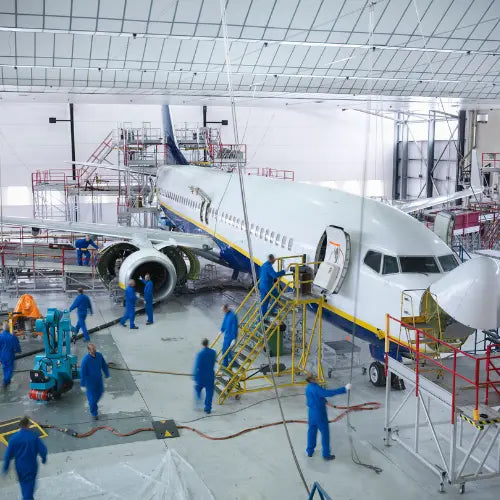
Image: Aircraft Engineers Conducting an A check Inspection
B Check
B checks are very similar to A checks, and most airlines and operators have merged these two routine checks to reduce downtime and optimize the maintenance technicians' time. This check is performed every 6-8 months and takes roughly 160-280 hours of labor to complete. Typical work completed during B checks includes checking alignment and torquing, landing gear, and any other potential issues that may have been missed during the A Check.

Image: Aircraft Engineers Inspecting Landing Gear
C Check
C check is performed approximately every 20-24 months but varies due to flight hours or according to the manufacturer's instructions. This check is much more thorough, and the inspection checks the majority of the aircraft's components. Due to the attention to small detail, more space is required to repair the aircraft therefore, this check usually takes place in a maintenance-based hangar. Completing a C check can take up to 6,000 hours of labor, putting the aircraft out of service for 1-2 weeks until all repairs are addressed.

Image: Aircraft Engineer Inspecting Engine
D Check or Overhaul
D checks are extensive overhauls, where the plane is essentially disassembled, inspected, repaired, and reassembled. D-level checks occur approximately every 6-10 years; however, this may change due to factors such as flight hours and engine type. Not only are the engines entirely disassembled, but the entire airplane interior is gutted to ensure the integrity of the metal skin of the aircraft has not been compromised. The process takes anywhere from 30,000-50,000 hours of labor, putting the aircraft out of commission for several weeks.

Image: Aircraft Engineer Inside Gutted Plane
Decisions to Repair/Overhaul
Maintenance A, B, or C checks often identify components or systems that must be repaired or overhauled. At that point the system or part in need of repair or overhaul will be moved to a different facility or another section of the same facility to perform the required work.
Due to aircraft complexity, repairs are often necessary to ensure optimal functioning. Any small or large component that shows signs of damage, deformation, corrosion, or missing parts during any of the checks mentioned previously must be replaced or repaired before an aircraft re-enters service.
A complete overhaul of an aircraft is considered a D check. As mentioned, the plane is disassembled to allow for a piece-by-piece inspection of the aircraft components to ensure that each part is still at optimal functioning. This process is not only labor intensive but can cost upwards of a few million dollars depending upon the extent of the overhaul. After about two or three overhaul maintenance routines, it becomes more cost effective to purchase a new aircraft. The old aircraft is then decommissioned and scraped for parts.
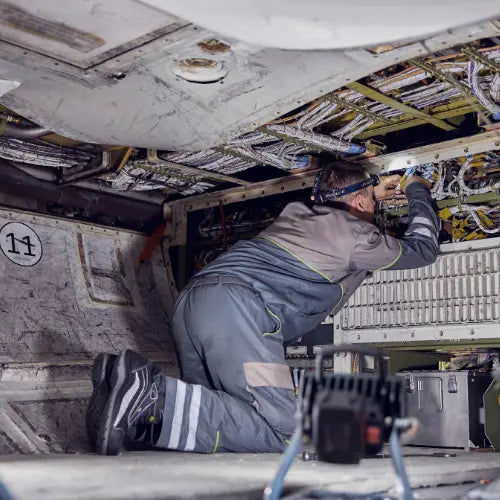
Image: Complete Overhaul being Performed on Plane
Why is MRO Important?
Safety is the top priority in aviation, and regular maintenance and timely repairs conducted through MRO help to guarantee potential issues are identified and addressed before jeopardizing flight safety. This proactive approach not only addresses wear and tear promptly but also reduces the risk of mechanical failures in flight. MRO enhances reliability, which is crucial for passenger satisfaction and minimizing costly delays and cancellations.
While MRO involves expenses, it ultimately saves money by preventing breakdowns and extending component lifespan. Moreover, efficient MRO practices optimize operational costs, contributing to airlines' financial sustainability. Finally, newer sustainable MRO practices are increasing, focusing on eco-friendly maintenance techniques such as material recycling, fuel optimization, and energy-efficient operations to reduce environmental impact.
The Future of MRO
The demand for MRO services is experiencing a significant surge both presently and in the foreseeable future. With the continuous expansion of air travel and older planes still in use, there's an increasing need to ensure the safety and reliability of aviation components. Recent, highly publicized issues with the Boeing 737 MAX have highlighted the importance of thorough maintenance, repair, and overhaul.
As regulations become stricter and safety standards rise, MRO providers face pressure to conduct more thorough inspections to detect even the smallest defects and maintain operational integrity. Advancements in technology are driving the adoption of more sophisticated inspection methods, amplifying the demand for MRO services.
InterTests Contribution to MRO in Aviation
MRO may operate behind the airline industry scenes, but its significance cannot be overlooked. MRO plays a vital role in keeping the skies safe and the planes flying. InterTest offers products that significantly aid the MRO process, ensuring that inspections and repairs are done accurately and efficiently.
Non-Destructive Testing (NDT) and Remote Visual Inspection (RVI) Solutions: NDT is a way of testing materials and components without altering or damaging them. InterTest offers cutting-edge NDT equipment that can help detect flaws or signs of wear in aircraft parts, ensuring that every component is thoroughly checked for integrity without compromising its usability.
The SeeUV Large Component Inspection Systems offer comprehensive fluorescent penetrant inspection (FPI) and magnetic particle inspection (MPI) NDT capabilities and are tailored to examine complex aircraft components such as aircraft engine shafts, drums, and spools. The SeeUV systems meet and exceed aviation component inspection standards, ensuring that even the most minor cracks and defects are detected to maintain the highest safety and operational integrity levels.


The key to any maintenance and repair task is the ability to see the problem. InterTest's RVI tools allow technicians to visually inspect hard-to-reach places within an aircraft's engine or body. Using high-definition video scopes, like the Yateks P+ Series Video Borescope, offers aviation MRO professionals the advantage of pinpoint accuracy in inspections, advanced documentation, and ability complete inspections of complex aircraft components in challenging environments.
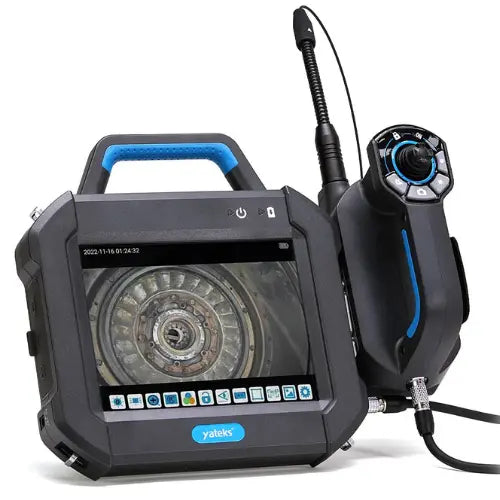
Image: The Yateks P+ Series Video Borescope
As technology advances, regulations evolve, and aircraft get older, the importance of MRO will only continue to grow, shaping the future of aviation for the better. InterTest is committed to innovation and excellence to ensure that MRO professionals can access the advanced tools necessary to meet today's challenges and anticipate those of tomorrow.
Contact us for more information about how our products can support your aviation MRO needs or to discuss custom solutions tailored specifically to your requirements.