In the realm of 21st-century manufacturing, the welding industry is experiencing a transformative shift thanks to technology innovations that are significantly improving precision, safety, and efficiency. Advances like TIP TIG’s enhanced wire feed technology, Novarc Technologies’ Spool Welding Robot, and Cavitar's laser illumination solutions are revolutionizing the field by increasing deposition rates, automating complex tasks, and delivering superior weld quality. These developments are pushing the boundaries in the welding industry, promising to redefine industry benchmarks for speed and performance.
Handheld GTAW Innovation

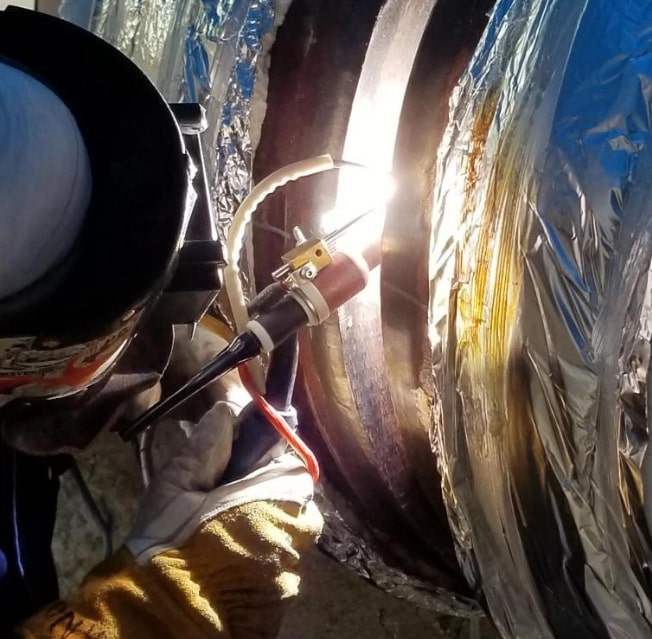
Traditionally, manual Gas Tungsten Arc Welding (GTAW), or often called TIG welding, is recognized for its high-quality welds and precise control. However, it often faces limitations in terms of deposition rates and welding speed. TIP TIG developed an innovative solution with its patented wire feed technology that induces a "vibratory" effect on the welding wire. These machines employ a four-drive roll mechanism that consistently feeds and oscillates the filler wire, controlled by a mechanized drive plate. This facilitates rapid oscillation of the filler wire, which works in conjunction with the hot wire feeding mechanism to provide several technical advantages.
The mechanical action of the drive plate induces vibrations in the wire, referred to as the "vibratory effect", that are transmitted into the weld pool, creating agitation and disrupting surface tension. This dynamic agitation is particularly beneficial for difficult alloys, such as stainless steel and duplex.

This approach enhances the welding process by combining the precision of traditional TIG welding with significantly improved deposition rates and reducing heat input. This increased deposition rate translates to faster weld speeds and greater productivity without compromising the quality of the weld. TIP TIG’s low heat input reduces the risk of heat-related issues such as warping or distortion, making it an ideal solution for thin materials and intricate welds.
Precision Automated Welding

Another company changing the welding industry is Novarc Technology. Older welding techniques required significant skill and practice, and with industry pioneers retiring and fewer people interested in learning the trade, manufacturers are increasingly struggling to find high-quality welders. Novarc Technologies developed the Spool Welding Robot to address this challenge by automating complex and repetitive welding tasks with precision and consistency.
Video: OverView of the NovEye™ - AI In Arc Welding
The design integrates established AI algorithms with advanced image processing to streamline the welding process, improve consistency, and enhance productivity. Utilizing extensive data collection and development, this unique software mimics the weld pool control of a skilled human welder, enabling the robot to handle repetitive welds.
The fully automated welding robot features real-time vision processing for adaptive optimization, and automatic multi-pass seam tracking for X-Ray quality welds every time, offering a significant advancement over traditional methods. This development represents a key innovation in automated welding, aiming to elevate industry standards for speed and quality.
Seeing Past the Arc

Image: Cavitar Camera on the Novarc Welding Robot
Guiding these new innovative welding techniques is the Cavitar Weld Viewing Cameras. These cameras utilize sophisticated optics, laser illumination, and band-pass to see past the blinding weld arc light, capturing previously unseeable images and videos. With different field of views, cabling configurations, and data transfer speeds, Cavitar cameras are suitable for the majority of welding applications including industrial and educational purposes. InterTest works with Cavitar and customers one on one to provide the best suited remote visual inspection solution for the customers unique application. InterTest offers unique camera configurations like the C400 Wide Weld Viewing Cameras and the Cavitar Welding Camera Training Kit - WeldMentor along with set-up assistance and in person demonstrations throughout the United States.
Find them at FABTECH
As these technologies continue to evolve, companies like Tip Tig, Novarc Technologies, and Cavitar are setting new benchmarks for precision, speed, and quality in welding. Their innovations are not only improving welding efficiency but push the boundaries of what is possible in manufacturing. To experience these transformative solutions firsthand and explore how they are shaping the future of welding, visit these industry pioneers at Fabtech, North America’s largest welding event October 15-17 2024.
Novarc Technologies - Booth W4062
InterTest, TIP TIG and Cavitar - Booth W4181